Welding joints, techniques, and expertise are used in a wide range of industries, from automotive and aerospace to manufacturing and shipping. Welders must be versatile in their knowledge of different types of welds and how to perform them, even if the welding required is not as comfortable as hoped.
Any great welder’s toolkit includes the ability to handle various welds and joints, but what are they and how do they differ? In this article, we will investigate and explain.
What exactly is Welding and Joints?
Before we proceed, let us first clarify this. Welding is the process of using heat to join two pieces of a material (in this case, metal). You create a weld to join points or edges on the basis of shape of material. As you might expect, there are only a few different ways to join two things together. All of the various angles and techniques are classified into five categories:
- The Tee Joint
- Joint at the Edge
- Joint at a Corner
- Joint Lap
- Joint of the Buttocks
Let’s take a closer look at each of these…
The Tee Joint
A Tee Joint, as the name suggests, is shaped like the letter T, with two pieces of metal welded together at a 90° angle. The edge is joined to a plate or a component with special care taken to ensure effective penetration into the weld’s roof.
A Tee Joint is a type of fillet joint (which we will discuss later), and there are several welding styles used to create Tee Joints:
- Fillet Welding
- Welding Plug
- Welding with Bevel-Groove
- Welding Slot
- Welding with a J-Groove
- Welding with a Melt-Through
- Welded Fare-Bevel-Groove
If the base metal is thick and still cannot support the load after welding on both sides, a groove-type weld will be used.
Tee Joints are not perfect because they are prone to Lamellar Tearing. When too much pressure is applied to a solid and inflexible joint, it cracks. A stopper can be used to prevent this in some cases, or the base metal quality can be improved.
Joint at the Edge
This is the most common type of sheet metal welding, especially where there are flanged edges (curved). It’s also a popular weld for connecting metal to adjacent pieces, such as if you have two quarter-pieces of a pipe and want to weld them together. You weld the top edge surface where the two adjacent pieces meet instead of the space between them. This type of weld helps to manage the stresses that the metal will face; however, depending on the metal’s application, it may be necessary to add filler metal for reinforcement.
Types of the stresses are as follows:
- Tensile
- Compression
- Bending
- Torsion
- Shear
Some joints can withstand greater forces than others, and it is these considerations that allow the welder to make their choice.
Various welding techniques used to create edge joints are as follows:
- Welding Square Grooves
- Butt Welding
- Welding with a J-Groove
- Welding with Bevel-Groove
- Welding with a V-Groove
- Welded U-Groove
- Welded Edge-Flange
- Welded Corner-Flange
Joint at a Corner
This, like the Edge Joint, is a popular method of welding sheet metal and is used when two pieces join at their outer edges to form a corner. The edges form a L shape when joined at right angles and are commonly used for welding boxes and frames.
This is not a strong weld because the two pieces of metal are prone to bending and misalignment, especially when the metal is thin or flexible. One way to strengthen the weld is to ensure that the joint is welded on all sides and not just one. Filler metal can also be used, but only in small amounts and at a lower thickness than the base metals.
Following is the list of welding techniques you can use to create a Corner Joint:
- Spot Welding
- Welding with a V-Groove
- Fillet Welding
- Welded U-Groove
- Welding with Bevel-Groove
- Welding Square Grooves
- Butt Welding
- Welded Flare-V Groove
- Welded Corner-Flange
- Welding on the Edge
- Welding with a J-Groove
It’s possible that you’ve noticed how similar a Tee Joint and a Corner Joint are. The location of the weld is what distinguishes them, with Tee Joints placed in the middle to effectively create two right angles.
Joint Lap
We can join two pieces of metal with different thickness using a Lap Joint. Some may argue that this type of joint should be called a ‘Overlap Joint,’ as the name is derived from how the two overlapping metal pieces are welded.
When the two pieces of metal are overlapped, they form two sections that must be welded together to strengthen the joint. It is recommended that both of these corners weld to give the weld the best chance.
Some welding styles for Lap Joints are as follows:
- Welding Plug
- Welding Slot
- Spot Welding
- Welding with a J-Groove
- Welding with Bevel-Groove
- Welded Flare-Bevel-Groove
- Joint of the Buttocks
Our fifth and final welding joint is the Butt Joint, which is probably the most common, inexpensive, and simple type of weld. In Butt Joint, you weld two pieces of metal end-to-end or side-by-side where the edges meet. The same theory applies to flat metal and pipes, as long as the welded edges match.
Butt Joint is also known as a ‘Square-Groove Weld,’ and it is used to join flanges, valves, fittings, and essentially any parallel pieces of metal in addition to flat metals and pipes.
This type of welding style is the basic and so it is the first welding style which most beginners learn. Following are its uses:
- Butt Welds with Square Grooves
- Butt Welds with V-Grooves
- Butt Welds with U-Grooves
- Butt Welds with J-Grooves
- Butt Welds with Flare-V Grooves
- Butt Welds with Bevels
- Butt Welds with Flare-Bevel-Groove
Joints for Fillet
The term ‘fillet’ appears several times in this article and is widely used in the welding industry. This is simply a collective term for Corner, Tee, and Lap Joints, which account for the vast majority of all welds. Fillet Joints require less preparation, are better for welding pipes, and are less expensive for the welder than Butt Welding. Butt Joints, on the other hand, use filler or excess material between the welded edges, whereas Fillet Joints use the filler material in the corners to create extra strength.
Take a look at the following infographic to see how these 5 welding joints appear:
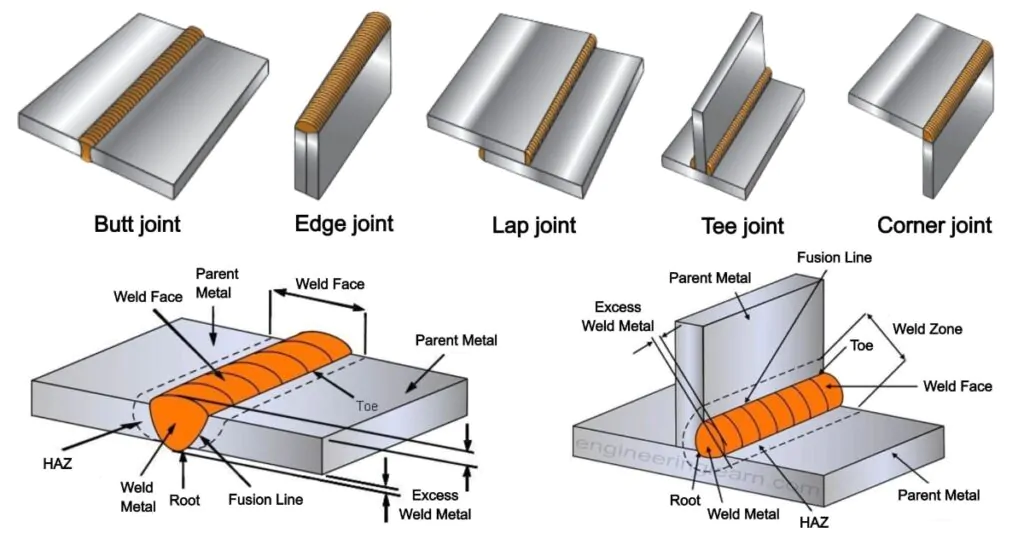
These are the top five basic types of welding joints that every newcomer to the trade should be aware of, but professional welders should also be aware of more advanced, specific, and complex welding joints. These Advanced Welding Joints differ depending on the sector in which the welder works; for example, the automotive industry uses aluminum, whereas the aerospace industry uses the TIG process for high-strength titanium joints.
Soldamatic’s extensive catalogue of 15 Advanced Welding Multi-joints, allows it to be suitable to train not only newcomers, but also professional welders.
It even allows companies to train their welders in specific welding joints, materials, and positions while reducing costs and risks by bringing real welding joints to Augmented Reality. If you want to learn more about Industrial Welding Multi-joints, please contact us.